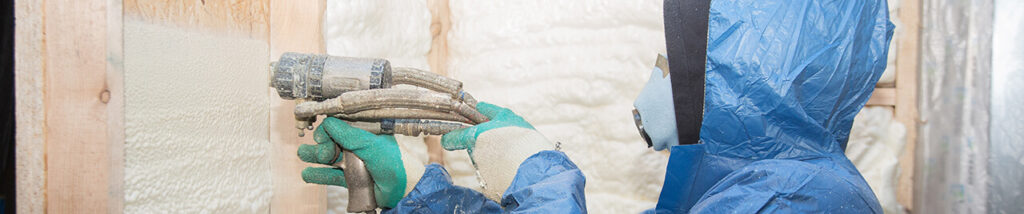
Spray-foam insulation can definitely crank up the performance of your home– if you make the ideal options. Here’s what to search for.
If a single item can declare the status of a green structure silver bullet, it might be foam insulation. Singlehandedly, these items can almost guarantee the highest useful R-value levels per inch, reliable air sealing, moisture management, and greater efficiency as broadening foam normally fills even hidden spaces; plus, foam remains less vulnerable to poor-quality installation, with the majority of jobs done by trained applicators.
But with considerable cost distinctions and subtleties in the performance characteristics and ecological impact of numerous foams, it’s crucial to comprehend the advantages and disadvantages of the fundamental foam items before choosing the best one for a specific project.
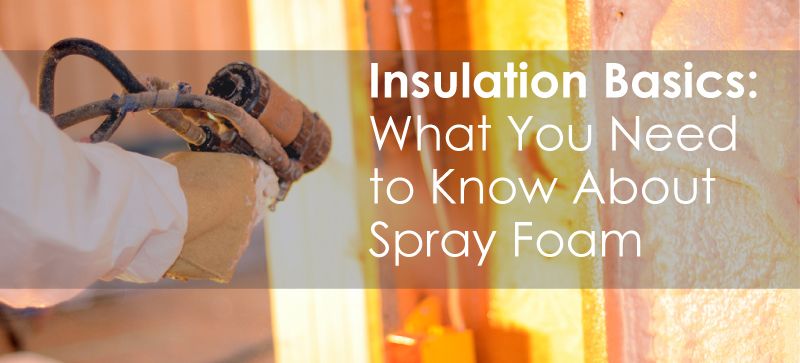
Foam Basics
If you’ve utilized a can of foam sealant, you already know the fundamentals: The insulation comes as a sticky, thick liquid that responds with air, broadening to flood any cavity you spray it into. Chemical additives in the foam insulation harden the expanding spume into a resilient, strong substance.
Because of this expanding quality, effectively used foam will normally fill every nook in a wall cavity, band joist, floor joist, and attic rafter so that the entire surface has a tight air seal. Given equal R-values, foam delivers about 20% to 40% better total performance than standard fiberglass or cellulose insulation, says Rick Duncan, technical director of the Spray Foam Alliance. The factor for this considerable difference, in spite of equal R-values, includes skilled installation and the integrated air seal.
Closed-cell foam insulation also handles moisture well enough to satisfy present ICC code requirements without an included interior vapor retarder in most applications. Perhaps most surprising, closed-cell insulation includes significant structural value, comparable to about 75% of the ultimate shear strength of a 1/2- inch sheet of plywood, according to Duncan.
On the other hand, spray-foam installation expenses between 100% to 300% more than professionally set up standard insulation systems. And from a green structure point of view, foam gets dismal marks in cradle-to-gate comparison, consisting of no to extremely low eco-friendly material or recycled material, compared to staple insulation products such as cellulose.
Many foam insulation is made with polyurethane, a two-part chemical structure that when combined produces gas bubbles, and then, like epoxy, sets up quickly, trapping the bubbles in a plastic matrix with outstanding insulating properties.
For the technical reader, polyurethane foam insulation arises from the reaction of diisocyanates blended with polyols. Chemicals, such as catalysts, surfactants, and flame retardants, may be added to control the set time, workability, and flame-spread attributes of the end product. It’s in the information of these chemical additives that foams separate themselves in both performance and ecological qualities.
Foams provide exceptional insulation and air seal; numerous fulfill Greenguard indoor air quality requirements and contain the most innovative propellants available without any effect on the ozone layer and enhancing international warming indices. Bio-based items have actually gone into the foam insulation market to balance out a few of the unfavorable effects, or at least perceived negative effects, of foam’s petroleum pedigree. However some misconceptions exist.
A common misunderstanding is that bio-based spray-foam insulations are made specifically from quickly eco-friendly plant sources, such as soybean oil, castor oil, and sucrose-based oils from sugar beets. But most items with bio-based content include less than 20%; in fact, the USDA’s limit for claiming spray foam is made with sustainable, bio-based products is only 7%. Nonetheless, the inclusion of plant oils decreases the petroleum content of foam insulation; national green requirements supply points for the use of foam insulation products that satisfy the requirements for the USDA’s Biobased Affirmative Procurement Program.
A research study of the ecological advantage of soy-based polyols commissioned by the United Soybean Board in 2004 concluded that every pound of soy polyol that changes a pound of petroleum has a favorable carbon benefit of 5.6 pounds; however, it stays a small element of foam insulation and some argue that the water and land consumed in growing crops, such as soybeans, has greater unfavorable environmental impact than the petro cost savings. Neither camp has conclusive evidence of considerable advantage or damage and the majority of claims in either case seem geared toward marketing instead of ecology. Overall, insulation of practically every type offers greater environmental advantages than costs.
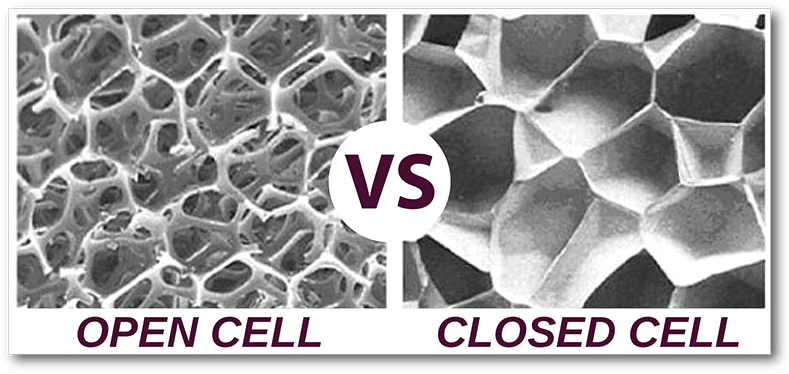
Open-Cell Vs. Closed-Cell
The real difference between kinds of foam insulation concentrates on whether they are open- or closed-cell. In general, both are made from the very same materials and work in the same way, trapping air or gas in a plastic matrix. The differences start with the “blowing representatives” utilized to produce bubbles and end with both varied performance and expense.
Open-cell foam costs somewhat less for the same thickness, but provides lower per-inch R-values than closed-cell items. In some circumstances, this is a downside, but where thickness is less pertinent, or where higher R-values are not required, then open-cell can offer the much better choice. It likewise has some green benefits over closed-cell: The blowing representative used to install open-cell insulation is water, which responds with air to become CO2– while closed-cell items use HFCs.
Due to the fact that CO2 expands quickly, the bubbles tend to burst prior to the plastic sets, and for this reason the “open cells,” which produce a spongy, light-weight foam. The market describes the foam as “half-pound” product, which just means the foam has a mass that weighs 0.5 pounds per cubic foot. This density yields an R-value of roughly 3.6 per inch, equivalent to many traditional insulations. Because of the open cell structure, open-cell foam permits some vapor to pass through, making it a good option in hot, damp environments, and under roof sheathing, such as in conditioned attics, where water vapor caught in between insulation and sheathing could promote wood rot.
In other words, open-cell foam, tested in accordance with ASTM E 283, offers an air barrier with vapor breathability. Water-blown solutions have less environmental impact than the present HFCs utilized for many closed-cell spray-foam insulation. And open-cell has about two times the sound decrease coefficient in regular frequency varies as closed-cell foam. Due to the fact that the blowing representative in open-cell insulation dissipates as it sets, instead of gradually in time, there is no degeneration of the R-value– a minor point offered aged closed-cell R-values still surpass open-cell R-values by a magnitude of nearly 100%.
Unlike open-cell foam, closed-cell foam utilizes chemical blowing agents that can be found in liquid form and become gasses as they are used. These gasses expand, however not as quickly as CO2, enabling the polyurethane plastic to set before the bubbles burst. This yields thick foam weighing almost 2 pounds per cubic foot, and without the capillary attributes of open-cell, it remains impermeable. The blowing representatives utilized carry out like the inert gasses in between the panes of high-performance windows, contributing to the insulating qualities of the foam. Unlike open-cell foam, closed-cell foam seldom needs any cutting, with little or no jobsite waste.
Closed-cell has more apparent benefits over open-cell, and a somewhat greater price (20% to 30% for the same density). It supplies both a vapor and air barrier and offers an aged R-value of a whopping 6.5 per inch. Because of its density and glue-like consistency, it stays extremely strong, supplying both compressive and tensile strength to structure similar to included sheathing, increasing the racking strength of walls by as much as 300%, according to the NAHB Research Center. Because water does not penetrate or deteriorate the item, FEMA recommends closed-cell foam as an appropriate insulation product for flood regions.
The principle drawback of closed-cell foam includes overkill. If you do not require the extra vapor barrier, structural strength, and R-value per inch, then you might be squandering money. As for the added wall strength, while real and substantial, it’s not acknowledged by building codes currently, so you can’t minimize the structural bracing as a tradeoff.
Environmental Tradeoffs
With the phase-outs of chlorine-based chemicals, third-generation blowing representatives such as Forane’s HFC-365mfc and Honeywell’s HFC-245fa have actually become commonly utilized in closed-cell foam, lowering concerns about ozone depletion. Although it no longer includes ozone-depleting chemicals, closed-cell foam still poses a high global warming capacity (GWP). The typical impact these days’s closed-cell foam blowing agents approaches 1,000 GWP versus 1 GWP for water-blown open-cell foam.
A current article in Environmental Building News argues against utilizing HFC-blown closed-cell insulation due to its high GWP. In computer system modeling referenced by EBN, the results revealed that closed-cell spray-foam insulation using HFCs can have lifetime GWP payback lengths of as much as 30 to 60 years with insulation depths from 1 to 4 inches, versus less than one year in all cases for cellulose.
Producer BASF states that the article doesn’t consider the air tightness achieved in a house with closed-cell spray-foam insulation, arguing that the relative efficiency advantages of this kind of foam in minimizing house energy consumption over the life time of the item surpass imbalances at the manufacturing and installation phase. The maker says a 3rd party– verified Eco Efficiency Analysis of its closed-cell polyurethane spray foam (which factored in the production, usage, and disposal phases) shows that cellulose insulation has more than twice the GWP than its closed-cell product over its lifecycle; the GWP for fiberglass was four times higher over its lifecycle.
In addition, new blowing representatives remain in advancement, with several chemical business anticipated to introduce fourth-generation blowing agents within the next 2 to 3 years, with no ozone depletion attributes and a significantly enhanced climate change profile of less than 15 GWP, according to Duncan. The EBN article acknowledges that this would alter the formula.
Recycling polyurethane foam provides another difficulty. As a thermoset product, it can not be melted or broken down into its parts for reuse. This indicates that even jobsite waste is tough to recycle, so correct setup with minimum overspray is vital to accomplish ecological effectiveness. Foam can be shredded and utilized as packing product or filler, however given that foam adheres to constructing structures and is difficult to extract and different from other materials throughout demolition, the labor, transportation, and processing expenses needed for reuse are not usually justified.
Harmful Blowing Agents and Fire Proofing
Totally cured polyurethane foam includes no residual off-gassing. Nevertheless, foam insulation includes harmful chemicals such as benzene and toluene, which position a possible risk issue throughout manufacture, transport, and installation. This is why installers must be trained and use protective equipment– a portion of the blowing agents in closed-cell foam dissipate throughout the installation, launching VOCs and greenhouse gases during application.
Producers no longer utilize polybrominated diphenylethers (PBDEs), synthetic fire-resistance chemicals that posture severe health and environmental risks, but concerns remain with their replacement. Many makers now use halogenated retardants that posture a health risk to installers and residents if the foam burns. Safer chemicals exist, such as triethyl phosphate (TEP), a non-halogenated fire retardant, and some producers are moving in this instructions.
No matter its petroleum makeup and toxicity throughout application, foam items supply such compelling toughness, air infiltration, moisture management, and energy-saving advantages that their usage continues to grow. Makers are working to keep improving their items from an ecological viewpoint, including a brand-new generation of high-density open-cell, water-blown foam.
Cost remains the most significant market barrier to more common use of foam in the structure market at large, however some contractors have actually found methods to obtain the benefits of foam while slashing off a few of the increased expense. For instance, some builders utilize a hybrid insulation system called “flash and batt,” applying 1 to 2 inches of closed-cell spray foam to a wall cavity very first followed by a standard fiberglass batt, cellulose, or, sometimes, even open-cell foam. This supplies the air-sealing advantages, with enhanced R-value, at lower expense. Some home builders utilize foam just in difficult-to-insulate locations, such as rim joists and eaves, where even the very best installers have problem matching the air seal and vapor-retardant qualities of foam.
Contact ArmorThane today and ask about their flagship foam application, ArmorFoam!