[imi_posts view=”grid” grid_column=”1″ filters=”” masonry_show=”1″ media_show=”1″ media_image_only=”1″ title_tag=”h3″ show_date=”1″ show_author=”1″ show_categories=”1″ show_comments=”1″ show_excerpt=”” more=”1″ number=”3″ img_size=”900×500″ pagination=”1″ css_animation=”none” style_radius=”5px”]
News
Table of Contents
REVIEWS YOU CAN RELY ON
Our Network
Spray foam insulation can crank up the performance of your homes—if you do it right. Check out our daily posts on the Foam Insulation and the Foam Insulation Market. We review each company and relay the information directly to you. Join our mailing list and have them sent directly to your email each and every day.
If you would like to know more about polyurea or spray foam, we recommend visiting ArmorThane
If you would like to know more about polyurea or spray foam, we recommend visiting ArmorThane
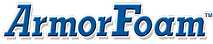
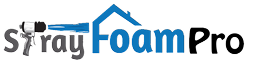
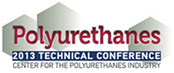
